The cordless power tool industry was transitioning to Lithium batteries from mature technologies such as NiCd and NiMh. Dewalt needed to deliver the highest energy density possible into the smallest package.
Company Stanley Black & Decker
Role Lead mechanical engineer
Product 20V Max 2.0Ah Lithium Battery (Dewalt DCB203)
Launched 2013
Manufacturing Location China
first to market
As a leader of innovation within the power tool industry, Dewalt works with major battery manufacturers to develop high-performance power cells. The industry was going through a shift from older, heavier battery technologies to lithium ion and lithium polymer. Dewalt was focused on offering the most run-time in the smallest package - the 2.0Ah battery.
power cells
New battery cells went through extensive internal verification testing before being built into packs. I worked closely with the cell testing team to identify leading candidates to be built into assemblies.
I developed lab and field testing of the 2.0Ah batteries with input from global compliance and reliability entities to ensure internal and external safety and performance standards were met.
more energy = more heat
A major tradeoff with packing higher energy density into the same footprint (18650 power cell) is the higher heat generated for a given application. Thus, my challenge was to develop a simple thermal management strategy which would optimize system performance and allow the full run-time to be realized by the user.
An extruded aluminum heat sink and thermal interface material was incorporated along with a custom bottom enclosure with a grid-like design. This provided passive cooling of the batteries as they heated up in heavy use applications by coupling the batteries directly to the aluminum. The heat was dissipated directly to the environment and the grid protected users from touching the warm heatsink.
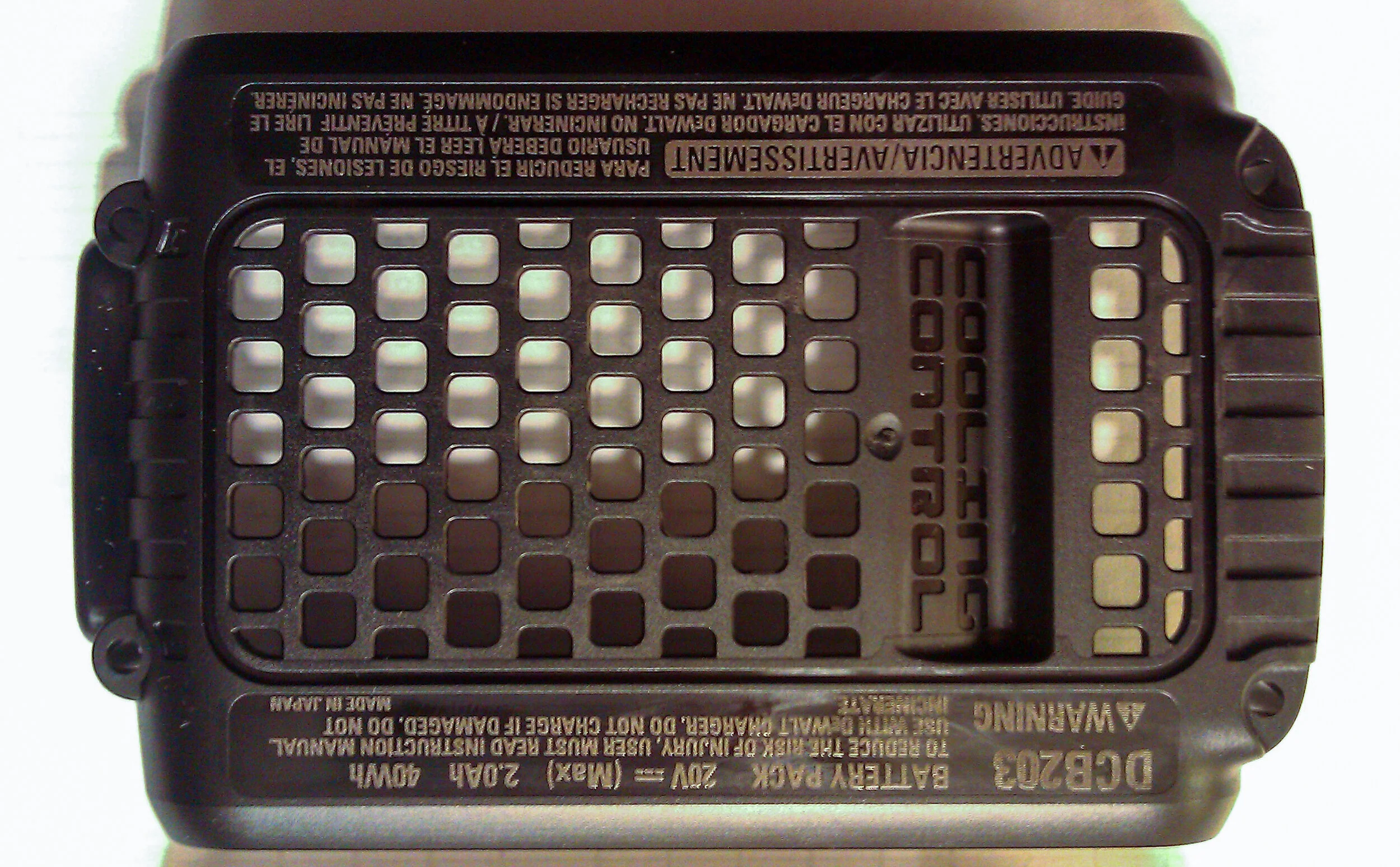
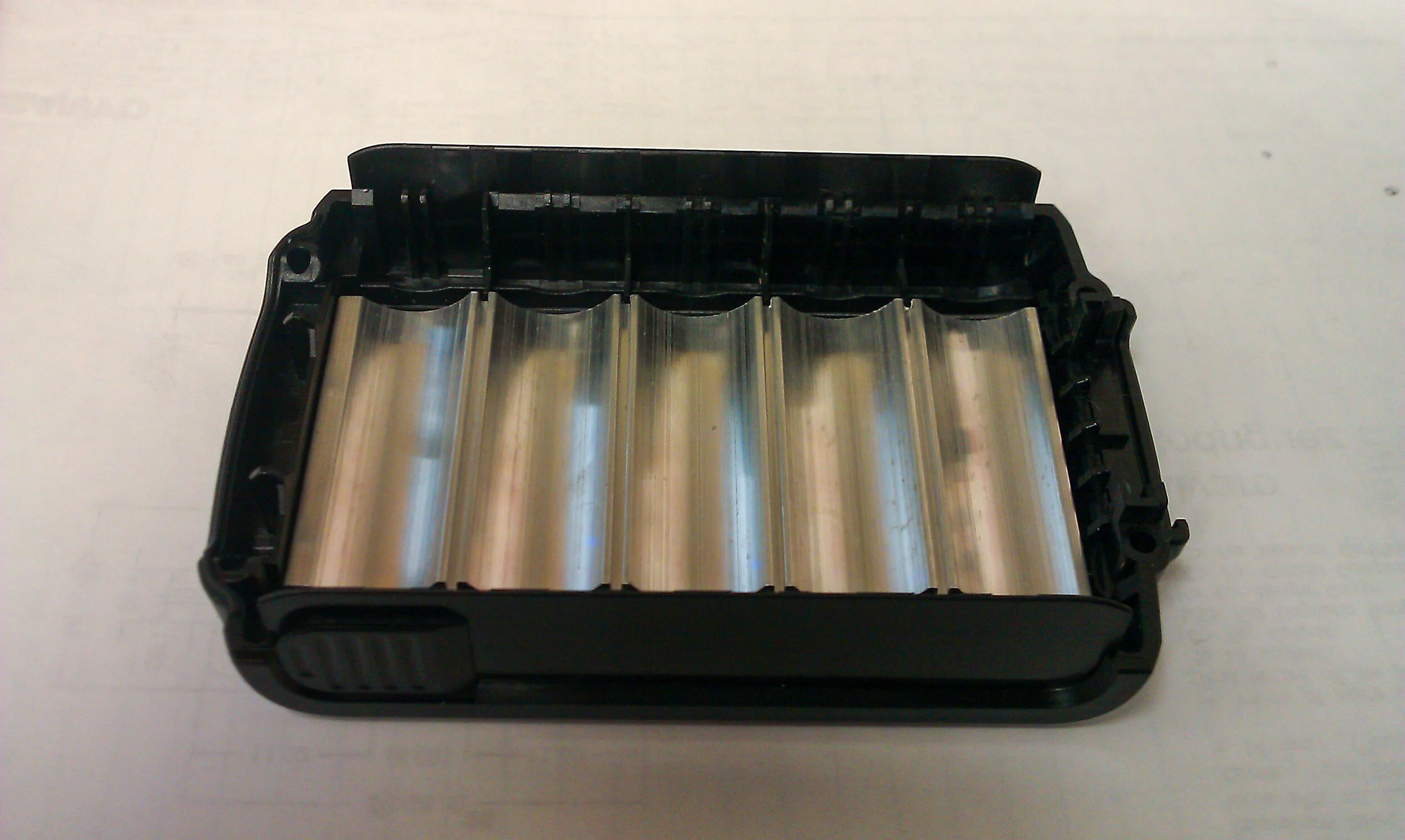